L’industria farmaceutica si basa su processi di tipo batch, ossia discontinui, che hanno lo scopo di originare differenti semilavorati e/o prodotti finiti.
La scelta della strumentazione e più in generale dei componenti della linea di produzione dell’aspirina, deve essere determinata tenendo in considerazione l’intera gamma di sostanze manipolate. All’elevata richiesta di flessibilità si aggiungono poi le fluttuazioni di mercato e le stringenti normative che regolano le emissioni dovute alle varie fasi del processo.
Introduzione all’industria farmaceutica
L’industria farmaceutica si occupa di scoprire, analizzare e produrre medicinali per la salute. Di estrema rilevanza sono le attività svolte dal gruppo R&D (Research and Development). Esse consentono di prevenire e di curare le malattie. In particolare, il progresso tecnologico registrato negli ultimi decenni ha consentito un notevole incremento delle scoperte scientifiche e il conseguente sviluppo di nuovi medicinali, sempre più specifici ed efficaci.
Allo stesso tempo, le case farmaceutiche, soprattutto quelle che operano su mercati internazionali, si ritrovano a dover rispettare numerose legislazioni e regolamentazioni riguardanti la produzione, l’approvazione, il controllo qualità e la vendita dei prodotti.
In aggiunta, molti dei processi eseguiti sono proprietari, non possono essere divulgati e vengono quindi sviluppati all’interno dell’azienda, aumentando di fatto la complessità dell’impianto da progettare.
Infine, il medicinale è spesso il risultato di una serie di passaggi nei quali possono essere coinvolte numerose sostanze, caratterizzate da stato (gas, liquido ecc.) e caratteristiche assai differenti (acido, base, conduttivo ecc.).
Complessivamente, la scelta della strumentazione e dei componenti del sistema deve essere svolta sulla base di molteplici fattori, tra questi vale la pena evidenziare i seguenti.
• Grado di flessibilità da ottenere per la gestione dei diversi semilavorati/prodotti
• Sostanze coinvolte nei processi (stato e proprietà chimico/fisiche)
• Facilità di movimentazione della strumentazione per adattare la linea di produzione al farmaco da realizzare
• Costo
• Domanda di mercato
• Controllo delle emissioni
Nella seguente sezione si presenta un esempio di processo farmaceutico che mira a descrivere la produzione dell’acido acetilsalicilico, più comunemente noto come aspirina.
Sintesi dell’aspirina
Le materie prime che consentono la sintesi dell’aspirina sono tre: l’anidride acetica, il mother liquor e l’acido salicilico in polvere. L’anidride acetica viene prevalentemente impiegata per effettuare la reazione chimica nota come acetilazione. Inoltre, è una sostanza da manipolare con cura poiché genera irritazioni, è infiammabile e corrosiva. Il mother liquor è invece un liquido recuperato durante il processo di sintesi dell’aspirina. In particolare, viene ottenuto dopo la fase di cristallizzazione, grazie a una tecnica di filtraggio. Il mother liquor è ricco di acido acetico, che è infiammabile e corrosivo, anche nei confronti dei metalli. L’acido salicilico è infine il componente principale dell’aspirina poiché funge da metabolita attivo del farmaco.
La rappresentazione schematica delle fasi principali del processo è riportata in Figura 1.
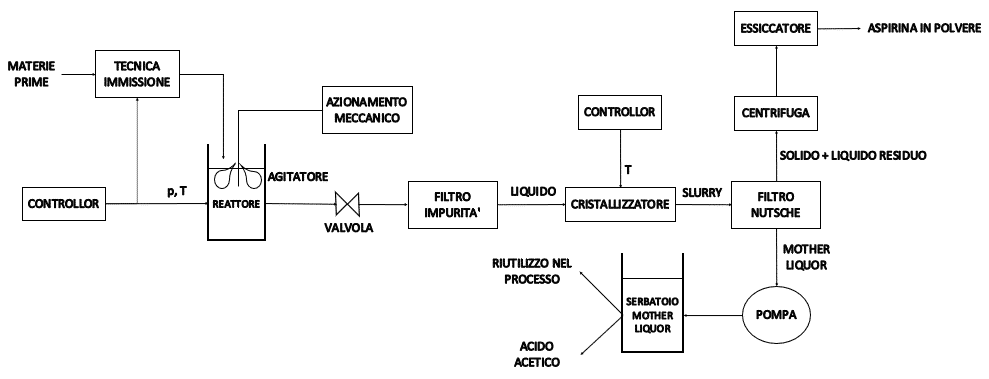
Il processo ha inizio con l’immissione delle materie prime all’interno del reattore, sede della reazione chimica. L’inserimento può avvenire in tre diverse modalità:
• Tramite gravità
I serbatoi sono posizionati ad un livello di altezza maggiore rispetto al reattore consentendo il passaggio di materia tramite il comando di una valvola di controllo in grado di regolarne la portata.
• Tramite pompa
La pompa è spesso adottata per ridurre la produzione di sottoprodotti indesiderati. In questo modo è infatti possibile conseguire un controllo accurato della concentrazione del materiale introdotto.
• Inserimento manuale
L’inserimento manuale è spesso usato per materiali solidi ed è reso possibile attraverso la movimentazione di una manopola.
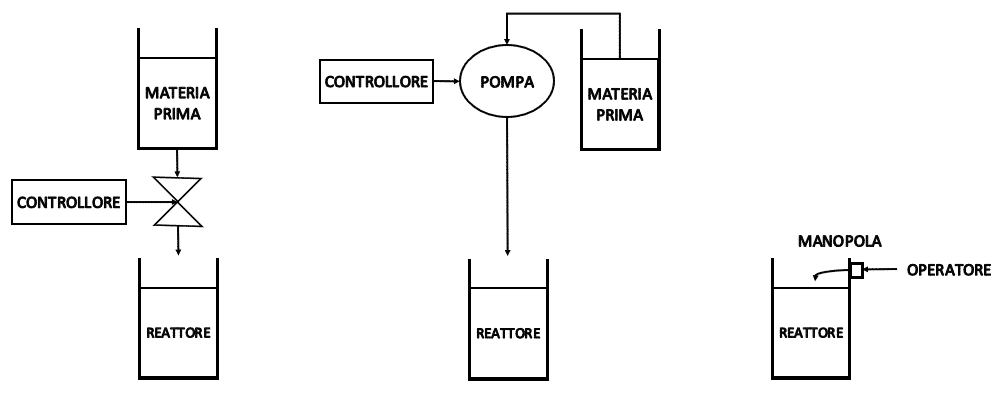
All’interno del reattore è presente poi un agitatore che, grazie a un azionamento meccanico, consente la regolazione del grado di miscelazione delle sostanze. Durante la fase di reazione sono fondamentali i valori di temperatura, pressione e velocità di aggiunta dei materiali registrati all’interno del reattore. Queste quantità sono spesso monitorate da sistemi di controllo in anello chiuso.
Per quanto riguarda l’aspetto termico, è possibile introdurre condotte contenenti liquidi refrigeranti e riscaldatori; mentre le altre due quantità sono in genere gestite da valvole e pompe di controllo. La reazione avviene così ad una data temperatura e per un certo periodo di tempo.
Come già anticipato nella sezione precedente, la scelta del reattore e dei suoi componenti è fondamentale non solo in termini di prestazioni, ma anche di materiali usati per la movimentazione in sicurezza degli acidi coinvolti nel processo. La strumentazione adottata deve infatti garantire la corretta esecuzione della reazione chimica. Inoltre, la richiesta di versatilità dell’impianto impone che i componenti siano facilmente rimovibili oppure riutilizzabili a temperature e pressioni di esercizio differenti e/o con sostanze con proprietà diverse.
Un altro fattore rilevante in fase di progettazione dell’impianto è definito dalle emissioni VOC (Volatile Organic Compounds). In questo caso è opportuno fare riferimento alle normative vigenti a livello nazionale e internazionale.
Ultimata la reazione, il prodotto, in forma liquida, viene scaricato dal reattore attraverso un’apposita valvola (oppure una pompa) e poi filtrato per eliminare le impurità presenti al termine di questa prima fase.
Il trasferimento del prodotto, una volta uscito dal reattore, può avvenire per gravità e con l’eventuale ausilio di valvole di apertura/chiusura. Segue quindi il processo di cristallizzazione durante il quale il prodotto viene raffreddato per un certo intervallo di tempo rendendo così la soluzione sovrassatura e consentendo la formazione di cristalli. Lo slurry risultante, ossia la miscela fluida di liquido e di solidi in sospensione, viene poi trasferito a un filtro Nutsche, grazie al quale si ricava il mother liquor raccolto in un serbatoio tramite un sistema idraulico di pompaggio.
Il mother liquor può eventualmente essere impiegato per recuperare dell’acido acetico. A valle del filtro Nutsche si trovano una centrifuga e un essiccatore che consentono di rimuovere il liquido residuo dal solido e di ricavare infine l’aspirina. I passaggi rimanenti sono il setaccio, la granulazione e la compressione delle polveri per ottenere le compresse vendute poi al pubblico.
Conclusioni
In questo articolo, sono state introdotte alcune delle tematiche da tenere presenti in fase di progettazione di un impianto farmaceutico. Sono stati evidenziati aspetti di carattere tecnologico come ad esempio la scelta della strumentazione. Allo stesso tempo, si è sottolineata l’importanza del fattore economico (richiesta di mercato e flessibilità di produzione). Si è concluso illustrando un esempio di processo per la produzione di un farmaco di largo consumo, ossia l’aspirina.